By Chris Kittleson, Director of Loss Control Technical Services - Public Risk Underwriters of Florida, Inc.
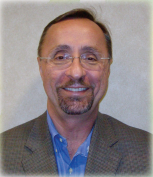
The safety and health of employees that work in Law Enforcement Property & Evidence (P&E) storage facilities are exposed to unique physical/environmental hazards. Due to the myriad of evidence that ranges from toxic drugs to blood soaked clothing, employees have the potential for exposures that are atypical to that of any other type of storage/ warehouse operations. In order to better understand these physical/environmental exposures, one must look at the design of the P&E storage facility, the proper containment/storage of evidence, as well as employee certification/training.
The most effective method of controlling employee physical/environmental hazards begins with the proper design of the P&E storage facility. In many instances the P&E storage facility was created using an existing space without consideration for proper ventilation, adequate lighting, fire-life safety equipment, sufficient storage space or natural disaster mitigation.
In this case, employees may be exposed to a variety of physical/environmental hazards with limitations placed on controlling the exposures and therefore protecting employee’s safety and health. The International Association of Property and Evidence (IAPE) has developed professional standards for the proper design of Property & Evidence storage facilities. Their website is located at – http://home.iape.org/
One of the most common problems that P&E storage facilities have is ventilation and its effect on indoor air quality. According to IAPE, the P&E storage facility should be ventilated in a manner that controls heat, cold, humidity and odors. In addition, any area that is used for storing drugs and/or biological mold producing materials should be independently ventilated in a manner that noxious fumes are removed from the building, and not re-circulated into the building’s heating, ventilation and air conditioning (HVAC) system. The proper design of this type of storage area should include a “negative pressure” ventilation system that changes the air in the P&E storage facility approximately 10-12 CPH (changes per hour).
With regards to adequate lighting, P&E storage facilities should be designed so that the facility is properly illuminated to reduce the potential for slip, trip and fall related hazards. In addition, emergency lighting should be provided so that employees can safely exit the storage facility during a fire and/or other emergency situations.
Fire prevention protocols dictate that the proper storage of incompatible chemicals/materials is of primary importance in controlling fire exposures. In addition to proper storage protocols, the P&E storage facility should be designed to include fire alarms, smoke detectors and fire sprinklers to effectively reduce the potential for fire and provide containment in the unlikely event of a fire.
Adequate storage space of a P&E storage facility has been challenged by the technological advances in the science of DNA. The ability to obtain DNA evidence from a multitude of items has resulted in a dramatic increase in the amount of evidence being stored and the length of storage time. In order to provide a less congested storage facility free of physical/environmental hazards the development and implementation of an effective and aggressive “Disposal Policy” for stored items is required. Continuous disposal of items not only assists in finding more available space, it also improves housekeeping practices which removes hazardous materials no longer needed for evidentiary purposes.
In concert with an effective “Disposal Policy”, packaging methods must be clearly defined, especially as it relates to hazardous materials. The following list is an example of the hazardous items commonly submitted to P&E storage facilities and should meet and/or exceed packaging standards developed by IAPE to protect employees.
• Ammunition
• Explosives/Fireworks
• Firearms
• Bio-hazardous materials
• Flammables
• Bladed/pointed weapons
• Hazardous materials
• Drugs
• Sexual assault evidence
• Syringes/sharps
In order to enhance employee awareness of P&E storage facilities physical/environmental hazards, appropriate certification/training should be provided. With regards to certification, IAPE provides for the courses leading to certification as a Certified Property and Evidence Specialist (CPES), which is available to Law Enforcement agency members. The CPES certification holder is a professional who has completed the requirements through training, has worked in the field for a required period of time and has demonstrated their knowledge of professional standards through successfully passing a written exam.
Please know that your Preferred Loss Control Consultant is available to assist members with the identification and control of P&E storage facility hazards.
Christopher H. Kittleson is the Director of Loss Control Technical Services and provides Loss Control services for public entities in the southeastern Florida region. With over 20 years of safety & health consulting experience Chris has developed industry expertise in the areas of Construction, Manufacturing, Fleet Safety and USL&H as well as safety programming expertise in the areas of Safety Program Development, Return to Work Programs, Regulatory Compliance, Accident Investigation and Safety Training. Chris graduated Cum Laude from St. Cloud State University, St. Cloud, MN with a Bachelors of Science in Engineering Technology, has earned his Associate in Risk Management (ARM), is a National Safety Council Certified Defensive Driving Course Instructor and Certified Playground Safety Inspector (CPSI), as well as a Professional Member of the American Society of Safety Professionals (ASSP), and was awarded the 2013 Safety Professional of the Year Award by the South Florida Chapter of ASSP.
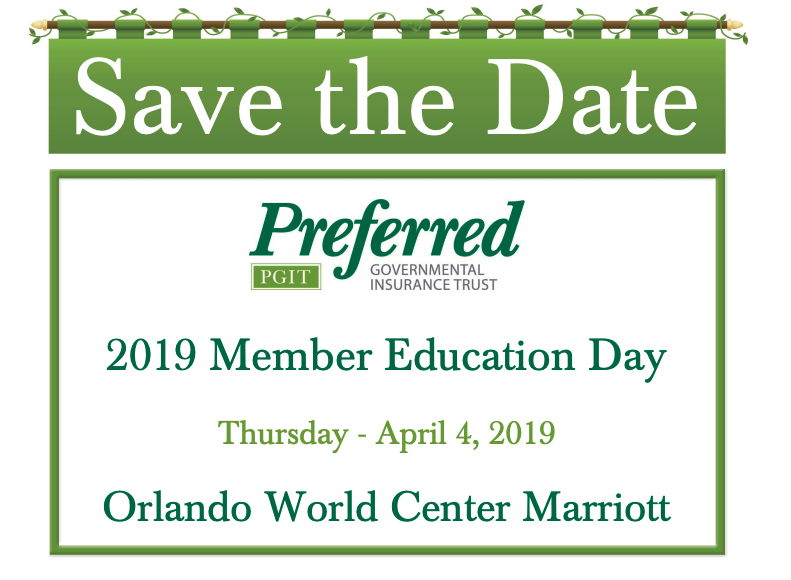