By Mike Marinan, Director of Member Services – Public Risk Underwriters of Florida, Inc
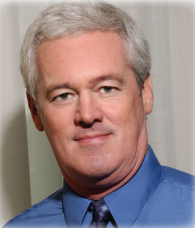
When an accident occurs it’s critically important to find out why it happened. Once you determine the why, you can implement measures to make sure that accident doesn’t happen again. When investigating a workplace accident, it’s important to remove the immediate hazard, such as a faulty piece of machinery or an unstable shelf. Even more crucial is figuring out the underlying cause of the problem.
A root cause analysis (RCA) helps you determine core issues that led to the accident. When you know the root cause(s), you can correct them to prevent similar incidents going forward. A root cause analysis refers to the process of identifying the underlying cause of an issue or incident. Whether you’re investigating an employee who crushed their foot when they dropped a heavy box or one who tripped over a cord in a poorly lit office, an RCA goes beyond simply removing the immediate cause of the accident.
Performed near the end of an accident investigation, RCAs aim to determine the true cause of the problem, rather than just addressing the symptoms. A root cause is a fundamental cause that, had it not been present, the issue wouldn’t have occurred. Identifying an accident’s root cause and eliminating it should prevent the issue from recurring.
So then, how do we identify the “root or true” cause of accidents? One common approach is called the “5 Why”. This technique begins with a problem statement and then starts asking the question “Why?” Why questions are repeated several times (generally around 5 times, thus the name of this technique), until the root causes become more apparent. Here’s an example:
Problem: An employee slips and falls in the Vehicle Maintenance Area
Q: Why did the employee fall?
A: He slipped on hydraulic oil that was on the floor
Q: Why was there hydraulic oil on the floor?
A: It leaked from the forklift while in operation.
Q: Why was the forklift used with a hydraulic oil leak?
A: The forklift operator didn’t know it was leaking.
Q: Why didn’t the forklift operator know it was leaking?
A: He didn’t check for oil leaks before operating the forklif.
Q: Why didn’t he check for oil leaks?
A: Because checking for oil leaks is not on the pre-operational inspection checklist that the operator completes each shift.
You can continue to go further, but at this point a root cause is emerging. Specifically, checking for oil leaks is not part of the forklift operator’s daily forklift inspection. A traditional investigation may find the cause to be “oil spilled on the floor” with the remedy limited to cleaning up the spill and instructing the worker to be more careful. A root cause analysis would reveal that the oil on the floor was merely a symptom of a more basic, or fundamental problem. From here, corrective actions become clear: update the forklift daily inspection checklist to include a check for oil leaks and train employees on this updated procedure.
Is this the only possible conclusion in this situation? The answer is no. In most cases, there could be several different responses for each step along the way. For instance, we could have said, the oil was on the floor because it leaked from the forklift AND because no one took the time to clean it up. We can then ask, “Why didn’t anyone take the time to clean it up?” and can continue down this other path to yet another root cause.
Accident Investigations that do not involve root cause analysis tend to address the symptoms of problems rather than the problems themselves. As such, corrective actions tend to be quick fixes that are not effective in preventing the problem from reoccurring. So, while Root Cause Analysis using the 5-Why Technique often takes more time, it is well-worth the effort. When root causes are identified, corrective actions are more effective, leading to a continuously improving and safer workplace. If you would like more information about RCA please contact your Preferred Loss Control Consultant and/or visit Training Network Now and view the streaming video on Accident Investigation.
Mike Marinan, Director of Member Services – Public Risk Underwriters of Florida, Inc. – Mike has a degree in Industrial Safety Engineering and over 37 years experience in the Safety and Risk Management field. He has been employed by Public Risk Underwriters of Florida, Inc. for 19 years. He holds an RMPE designation, holds a General Lines 220 and 218 licenses, is an active member of Central Florida PRIMA, as well as an active member of ASSP and numerous related Safety and Health organizations. He was a Governor appointee to the Task Force on Workplace Safety.